CHIC’s Head of Development, Sarah Davey, explores the world of Modern Methods of Construction (MMC) and its potential impact on the housing sector. Despite years of discussion, MMC has struggled to gain traction in housing, emphasised with this years collapse of key sector providers, including those with Homes England support, like L&G and Ilke Homes. These have exacerbated the sectors loss of confidence in MMC as a mainstream solution.
Modern Methods of Construction (MMC) has been a political favourite as a solution to our housing crisis for quite some time. Despite the extensive support, there has been minimal adoption, particularly in the affordable housing sector. In 2018 CHIC exhibited a modular showhouse at the Manchester Housing Conference (with Ilke), showing how high quality housing could be developed and transported effectively. Six years on though there has been limited progress with demand.
What Exactly Is MMC and What Does It Entail?
MMC encompasses seven categories of construction, primarily defined by their specific methods. These include fully modular housing ‘units’ manufactured in a factory and frame and panel systems made of timber or metal, which are produced in a factory and then transported to the construction site for assembly. Others includes fitted room modules (kitchens and bathrooms) and pre-manufactured components.
What Are the Main Issues With MMC
To understand the constraints of MMC we need to understand the issues:
1. Factory built fully modular is not suitable for all sites and is more suited to standard house types for low rise housing.
2. Difficult to reach or narrow access sites do not work for factory built units, as the modules are delivered by large trucks and need mobile cranes to position them.
3. Factory manufacturing is only financially viable with high volumes – so, a sustained order book is key. Producing just a few houses is not cost effective for a production line, particularly if there are multiple design variances.
4. MMC is fundamentally a manufacturing process, not construction. This distinction is often overlooked, but needs to be understood at the very beginning of the development process, to influence design and programming.
5. The funding mechanisms for MMC differ from traditional construction. Materials need to be paid for at the point of supply, making funders nervous since this upfront payment can be viewed as ‘at risk’, when in another organisation’s factory. While vesting agreements can mitigate risk, they still demand cash flow.
6. Many manufacturers fail due to insufficient demand for their products. The slow planning system and cyclical nature of housing confidence do nothing to help generate a sustained order book.
7. The main survivors in the MMC industry are larger manufacturers offering diverse products across multiple sectors, including education, hotel accommodation and housing. Frame and panel manufacturers are also thriving because their construction methods closely resemble traditional construction, but with added benefits – and they can service higher building designs, with more design repetition.
8. Benefits include rapid frame erection and weatherproofing, allowing buildings to become watertight within days. This enables internal fit-out to progress simultaneously with external work. For metal frame and panel manufacturers, the entire external fabric, including windows and doors, is completed in the factory, resulting in quicker build programmes and reduced exposure to weather-related delays.
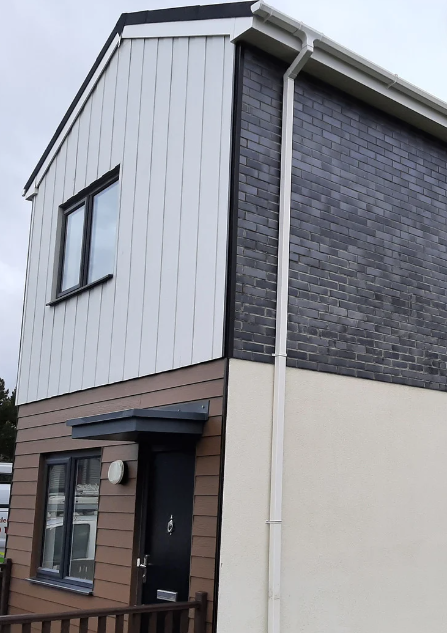
Conclusion
There is a place for MMC in housing, but it will not become mainstream in fully modular buildings until the market fully understands its processes and benefits. The immediate future of MMC lies in frame and panel construction, which can easily be substituted for traditional building methods and is already widely used.MMC manufacturers are already meeting building regulation Part L, meaning their build costs will not increase as much as those for traditional construction. As energy efficiency standards for new homes continue to evolve, MMC offers a viable path forward.
If we are to solve the housing crisis, capacity needs to increase in a market with significant pressures on construction skills. MMC can deliver, but for it to do so the supply of land and planning system need a radical overhaul, to generate sustained order books. The new government have provided this overhaul, so lets hope they deliver.
How CHIC can help
After thorough consultation with our members and supply chain partners, CHIC understood that the newbuild development market isn’t one size fits all.
Therefore, our recently launched Newbuild Development Framework provides a comprehensive solution to deliver all types of development related works and services from small infill and garage sites to large estate regeneration projects including newbuild, refurbishment/retrofit and cross subsidy housing for sale. It also provides MMC solutions including fully modular, frame & panel and turnkey options so that we can be progressive as a sector, but also take into consideration current behaviors and needs. Find out more here: https://www.chicltd.co.uk/services/frameworks/newbuild/